How to Choose the Best Custom Compression Spring Manufacturer for Your Project
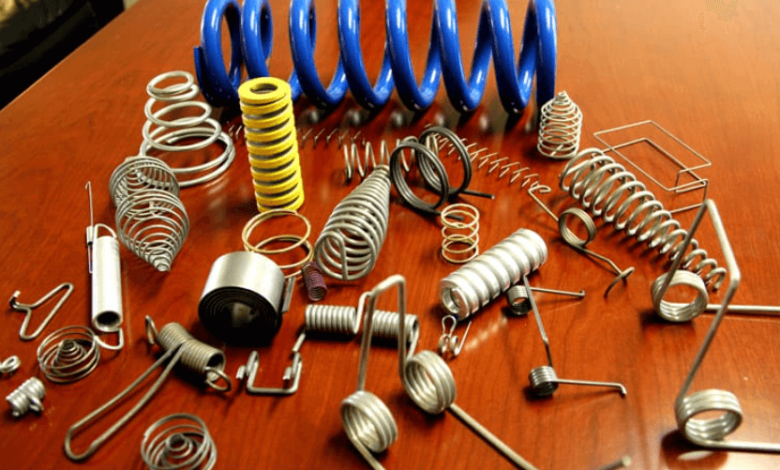
Compression springs are fundamental mechanical components that play a vital role in countless devices and industrial applications. When off-the-shelf springs cannot meet specific performance or design requirements, turning to a custom compression spring manufacturer becomes necessary. Custom springs offer tailored solutions that optimize functionality, durability, and space utilization.
This article explores the critical aspects of selecting a custom compression spring manufacturer, the manufacturing process, the benefits of custom springs, and tips for establishing a strong partnership with your supplier.
What Are Custom Compression Springs?
Custom compression springs differ from standard springs because they are designed and produced to meet precise specifications rather than generic standards. These springs are made to fit unique size constraints, load requirements, and environmental conditions, ensuring optimal performance in specialized applications.
Key characteristics that can be customized include:
- Wire diameter and material
- Outer and inner coil diameter
- Number of coils and pitch
- Free length and solid height
- Surface finish and protective coatings
See also: Business Payments With General Interbank Recurring Order
Why Work with a Custom Compression Spring Manufacturer?
1. Precise Engineering to Meet Exact Needs
A custom compression spring manufacturer works closely with engineers to design springs tailored for exact load capacities, space constraints, and durability requirements. This precision ensures the spring functions flawlessly within the target assembly.
2. Access to Specialized Materials and Treatments
Manufacturers experienced in custom springs can recommend and supply a wide variety of materials, including stainless steel, music wire, Inconel, or phosphor bronze. They also offer heat treatments and surface coatings that improve resistance to corrosion, wear, and fatigue.
3. Enhanced Quality and Reliability
Custom manufacturing processes emphasize tight tolerances and rigorous quality control, leading to springs with consistent mechanical properties and longer service lives.
4. Solutions for Complex Applications
Certain industries — aerospace, medical, automotive — require springs that meet stringent safety and performance standards. Custom compression spring manufacturers have the expertise to deliver springs compliant with industry certifications and regulations.
Understanding the Custom Compression Spring Manufacturing Process
Step 1: Design and Engineering Consultation
The process begins with detailed consultation to define the spring’s functional requirements, including load, deflection, dimensions, and environmental factors. Manufacturers use computer-aided design (CAD) software and simulation tools to optimize spring geometry.
Step 2: Material Selection
Choosing the right material is essential. The manufacturer considers factors such as strength, fatigue resistance, corrosion tolerance, and temperature range.
Step 3: Precision Coiling
Using CNC coiling machines, wire is formed into helical shapes with exact diameters and pitches. This step is crucial for maintaining consistent spring rate and load capacity.
Step 4: Heat Treatment
Springs are heat treated to relieve internal stresses and improve mechanical performance, ensuring elasticity and strength.
Step 5: Surface Finishing
Coatings such as zinc plating, powder coating, or passivation protect springs from environmental damage and improve lifespan.
Step 6: Quality Assurance and Testing
Springs undergo dimensional inspections, load testing, and fatigue analysis to verify conformity to specifications. Reputable manufacturers provide detailed test reports and certifications.
Benefits of Partnering with an Experienced Custom Compression Spring Manufacturer
Superior Product Performance
Custom springs designed and manufactured to exact specifications perform better in their application, reducing the risk of failure.
Cost Savings Over Time
Though custom springs may have higher initial costs than standard options, they minimize downtime, maintenance, and product recalls, resulting in long-term savings.
Innovation and Flexibility
Experienced manufacturers assist with design improvements and prototyping, enabling faster iteration and innovation.
Reliable Supply Chain
A trusted manufacturer manages inventory and production schedules effectively to ensure timely delivery, critical for production continuity.
Industries That Rely on Custom Compression Spring Manufacturers
- Automotive: Springs used in suspension systems, engine components, and safety devices demand custom solutions for reliability and durability.
- Aerospace: High-performance springs withstand extreme conditions and are designed for weight reduction without compromising strength.
- Medical: Springs in surgical instruments and implantable devices require precision manufacturing and biocompatible materials.
- Industrial Machinery: Springs absorb shocks and maintain force in equipment operating under heavy loads.
- Consumer Electronics: Compact, precise springs enable responsive buttons and compact assemblies.
How to Choose the Right Custom Compression Spring Manufacturer
Evaluate Industry Experience
Look for manufacturers with proven experience in your sector and with similar spring applications.
Review Certifications and Quality Systems
ISO 9001 and industry-specific certifications ensure the manufacturer follows high-quality standards and consistent processes.
Assess Material and Technological Capabilities
A broad material portfolio and investment in advanced manufacturing equipment (e.g., CNC coilers, automated testing) indicate technical strength.
Consider Customer Service and Technical Support
Manufacturers who provide engineering support and flexible production runs help ensure your project’s success.
Ask for References and Samples
Testing sample springs can validate quality and performance before placing large orders.
Best Practices for Working with Your Custom Compression Spring Manufacturer
- Clearly communicate all technical requirements and constraints upfront.
- Engage the manufacturer early in the product development process for design input.
- Request prototypes and validate performance through testing.
- Maintain open communication for updates, feedback, and modifications.
- Plan for long-term collaboration to optimize pricing and supply reliability.
Conclusion
A skilled custom compression spring manufacturer is a vital partner for businesses requiring high-performance springs tailored to unique applications. By working closely with such manufacturers, companies gain access to precision-engineered springs that meet exact specifications, withstand demanding environments, and contribute to product success.
Careful selection based on experience, quality, technical capabilities, and customer support ensures your custom compression springs will deliver reliability, efficiency, and innovation in your projects. Investing in a trusted manufacturer ultimately leads to superior products, cost savings, and sustained competitive advantage.