Exploring the Double Pig System Working Principle: Precision and Efficiency in Modern Pigging
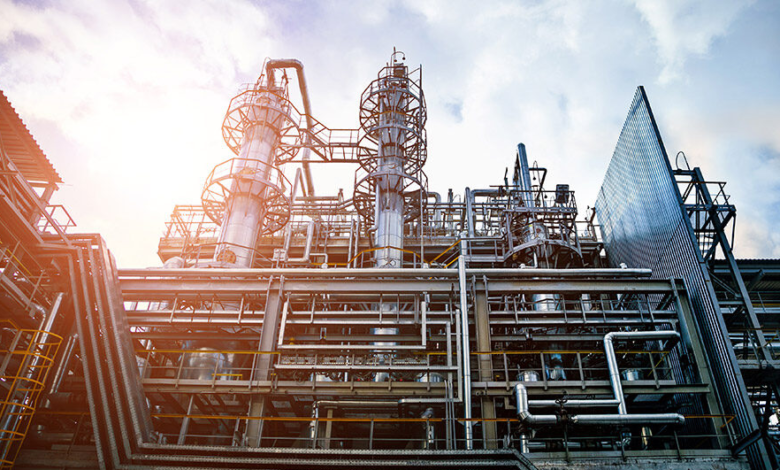
In the world of fluid handling, manufacturers face increasing pressure to reduce waste, increase efficiency, and maintain hygiene across product lines. These goals are especially critical in industries like food and beverage, cosmetics, pharmaceuticals, chemicals, and paints, where precision and cleanliness directly impact product quality. A solution that is gaining widespread recognition is the double pig system—an advanced pipeline cleaning and product recovery technology. This article dives into the double pig system working principle explaining how it functions, its advantages, and why it is transforming modern production processes.
What Is a Double Pig System?
A double pig system is a form of pigging technology that utilizes two pipeline pigs in a controlled sequence to recover product and clean pipelines. Pigs are devices made from flexible, hygienic materials designed to tightly fit within a pipe and move through it, pushing out product or debris.
While single-pig systems are commonly used to clear lines, the double pig system offers enhanced control and cleanliness by isolating the product slug between two pigs. This setup is ideal for high-value liquids, sensitive formulations, and systems requiring reduced cross-contamination.
The Double Pig System Working Principle
The double pig system working principle centers around encapsulating a volume of product between two pigs. These pigs act as mobile barriers, driven by a pushing medium (such as air or nitrogen), allowing the product to be moved through the pipeline without mixing with other fluids or residues.
Here’s a step-by-step overview of how the double pig system works:
1. Pig Loading
Two pigs are inserted into the pipeline via a specially designed pig launcher. The first pig (front pig) enters first, followed by the desired amount of product. Then, the second pig (rear pig) is launched to trap the product between the two pigs.
2. Encapsulation of Product Slug
Once both pigs are in the pipeline, a specific volume of product becomes isolated between them. This ensures that the product remains clean and free from external contamination as it moves through the line.
3. Pushing Medium Applied
Compressed air, nitrogen, or another safe medium is applied behind the second pig. This drives both pigs forward simultaneously, with the encapsulated product moving neatly between them.
4. Travel Through the Pipeline
The pigs maintain tight contact with the pipeline’s internal walls. As they travel, they push out any residual product while carrying the encapsulated slug to the desired endpoint.
5. Receiving and Product Discharge
At the pipeline’s end, a pig receiver collects both pigs, and the product is dispensed into a filling line, tank, or packaging system. Sensors and automation can control the process for maximum precision.
This systematic, controlled process is what defines the double pig system working principle—one that enhances product yield, cleanliness, and operational safety.
See also: Huawei Mate XT: Redefining Mobile Technology
Key Components of the Double Pig System
To function effectively, a double pig system includes several critical components:
- Pig Launcher and Receiver: Mechanisms to safely introduce and remove pigs from the pipeline.
- Pigs: Flexible, sanitary-grade devices made to fit snugly inside the pipe.
- Control Valves: Piggable valves that allow free movement of pigs without obstruction.
- Compressed Gas Supply: Provides propulsion for the pigs and product slug.
- Sensors and PLCs: Automated systems to monitor and control the pigs’ location and movement.
All these components must be precisely engineered and compatible with the specific fluid and operational environment.
Benefits of the Double Pig System
Understanding the double pig system working principle helps reveal why it is rapidly becoming the go-to solution for efficient product transfer:
✅ High Product Recovery
One of the most significant advantages is the ability to recover over 99.5% of product from pipelines. This drastically reduces waste, especially important for expensive or specialty products.
✅ Reduced Cross-Contamination
Because the product slug is isolated between two pigs, there is minimal risk of mixing between different product batches. This is crucial for industries where allergen control or formulation accuracy matters.
✅ Improved Hygiene
The pigs clean the pipe walls as they travel, reducing microbial risks and simplifying compliance with food and pharmaceutical standards.
✅ Faster Product Changeovers
Operators can switch between products more rapidly since less cleaning and downtime are required between batches.
✅ Lower Environmental Impact
With less need for water and cleaning agents, the system supports sustainability by reducing chemical waste and water consumption.
Industrial Applications
The double pig system is suitable for a wide range of sectors:
- Food & Beverage: For viscous sauces, yogurt, and syrups where hygiene and product loss are concerns.
- Cosmetics: In transferring creams, shampoos, and gels without cross-contamination.
- Pharmaceuticals: For syrups and sterile fluids that require high purity.
- Paints & Chemicals: Preventing mixing of hazardous or colored materials during product transitions.
Conclusion
The double pig system working principle represents a significant advancement in pipeline product recovery and hygiene. By isolating and propelling product between two pigs, the system offers exceptional product yield, cleanliness, and process efficiency. Whether you’re producing food, pharmaceuticals, or chemicals, adopting this technology is a strategic investment in quality, sustainability, and profitability.
As industries move toward smarter, cleaner operations, the double pig system stands out as a modern solution that delivers measurable benefits. Understanding its working principle is the first step in unlocking its full potential for your production line.