Ensuring Workplace Safety: Essential Measures
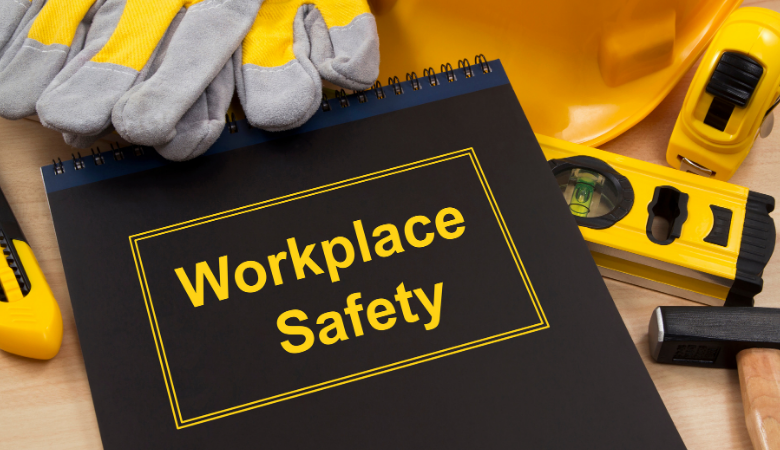
Workplace safety is a fundamental aspect of any organization, transcending mere compliance with regulations to encompass the well-being of employees and the overall productivity of the business. A safe work environment not only protects employees from physical harm but also fosters a sense of security and trust within the workforce. When employees feel safe, they are more likely to be engaged, motivated, and productive.
This connection between safety and productivity is supported by numerous studies that indicate a direct correlation between a safe workplace and enhanced employee morale. For instance, organizations that prioritize safety often experience lower turnover rates, as employees are more inclined to remain with a company that values their health and well-being. Moreover, the financial implications of workplace safety cannot be overlooked.
Accidents and injuries can lead to significant costs for businesses, including medical expenses, legal fees, and lost productivity. According to the National Safety Council, workplace injuries cost U.S. employers over $170 billion annually.
This staggering figure highlights the importance of investing in safety measures as a means of reducing potential liabilities. By implementing effective safety protocols, organizations can mitigate risks and avoid the financial repercussions associated with workplace accidents. In essence, prioritizing workplace safety is not just a moral obligation; it is a strategic business decision that can lead to long-term success.
Risk Assessment and Hazard Identification
Risk assessment and hazard identification are critical components of an effective workplace safety program. The process begins with a thorough evaluation of the work environment to identify potential hazards that could pose risks to employees. This involves examining various factors, including equipment, materials, processes, and even the physical layout of the workplace.
For example, in a manufacturing facility, risk assessment might reveal hazards such as moving machinery, exposure to toxic substances, or slip and fall risks due to wet floors. By systematically identifying these hazards, organizations can take proactive measures to mitigate them before they result in accidents. Once hazards have been identified, the next step is to assess the level of risk associated with each one.
This involves evaluating the likelihood of an incident occurring and the potential severity of its consequences. For instance, a chemical spill in a laboratory may present a high risk due to both the likelihood of exposure and the potential for serious health effects. Conversely, a cluttered workspace may pose a lower risk but still requires attention to prevent minor injuries.
By prioritizing risks based on their severity and likelihood, organizations can allocate resources effectively and implement targeted interventions that address the most pressing safety concerns.
Employee Training and Education
Employee training and education play a pivotal role in fostering a safe workplace environment. It is essential for organizations to provide comprehensive training programs that equip employees with the knowledge and skills necessary to recognize hazards and respond appropriately. Training should cover a wide range of topics, including proper equipment usage, emergency response procedures, and personal protective equipment (PPE) requirements.
For example, in a construction setting, workers must be trained on how to operate heavy machinery safely and understand the importance of wearing hard hats and safety goggles to protect against potential injuries, and using products from AMCO safety matting. Moreover, ongoing education is crucial for maintaining a culture of safety within the organization. Safety training should not be viewed as a one-time event but rather as an ongoing process that evolves with changes in the workplace.
Regular refresher courses can help reinforce safe practices and keep employees informed about new regulations or procedures. Additionally, organizations can benefit from incorporating hands-on training exercises that simulate real-life scenarios, allowing employees to practice their skills in a controlled environment. This experiential learning approach not only enhances retention but also builds confidence among employees when faced with actual safety challenges.
Implementation of Safety Protocols and Procedures
The implementation of safety protocols and procedures is essential for translating safety policies into actionable steps that employees can follow. These protocols should be clearly documented and easily accessible to all staff members. For instance, an organization may develop specific safety procedures for handling hazardous materials, including guidelines for storage, labeling, and disposal.
By providing clear instructions, employees are better equipped to adhere to safety standards and minimize risks associated with their tasks. In addition to written protocols, organizations should establish mechanisms for monitoring compliance with safety procedures. Regular audits and inspections can help identify areas where protocols may not be followed or where improvements are needed.
For example, if an inspection reveals that employees are not consistently wearing required PPE, management can take corrective action by reinforcing the importance of compliance through additional training or disciplinary measures if necessary. Furthermore, involving employees in the development of safety protocols can enhance buy-in and accountability, as they are more likely to adhere to procedures they helped create.
Regular Maintenance and Inspection of Equipment
Regular maintenance and inspection of equipment are vital components of workplace safety that often go overlooked. Equipment failure can lead to serious accidents and injuries; therefore, organizations must establish routine maintenance schedules to ensure that all machinery and tools are functioning properly. This includes not only routine checks but also preventive maintenance designed to identify potential issues before they escalate into dangerous situations.
For example, in an industrial setting, regular inspections of conveyor belts or forklifts can help detect wear and tear that could lead to malfunctions. In addition to scheduled maintenance, organizations should also implement a system for reporting equipment issues promptly. Employees should feel empowered to report any concerns regarding equipment functionality without fear of reprisal.
This open line of communication is crucial for maintaining safety standards; it allows for quick action to be taken when problems arise. Furthermore, keeping detailed records of maintenance activities can help organizations track equipment performance over time and identify patterns that may indicate underlying issues requiring attention.
Creating a Culture of Safety within the Workplace
Creating a culture of safety within the workplace is perhaps one of the most significant challenges organizations face. A culture of safety goes beyond policies and procedures; it encompasses the attitudes and behaviors of all employees regarding safety practices. Leadership plays a critical role in shaping this culture by demonstrating a commitment to safety through their actions and decisions.
When management prioritizes safety in their daily operations and communicates its importance consistently, it sets a tone that resonates throughout the organization. Engaging employees in safety initiatives is another key aspect of fostering a culture of safety. Organizations can encourage participation by forming safety committees or conducting regular safety meetings where employees can voice concerns and share suggestions for improvement.
Recognizing and rewarding safe behavior can also reinforce positive practices; for instance, implementing incentive programs that acknowledge teams or individuals who demonstrate exceptional commitment to safety can motivate others to follow suit. Ultimately, cultivating a culture of safety requires ongoing effort from all levels of the organization, creating an environment where everyone feels responsible for maintaining a safe workplace. In conclusion, workplace safety is an integral part of organizational success that encompasses various elements such as risk assessment, employee training, protocol implementation, equipment maintenance, and cultural development.
By prioritizing these aspects, organizations can create safer environments that protect their most valuable asset—their employees—while also enhancing productivity and reducing costs associated with workplace incidents.