Precision in 3D Printing: Understanding Fit and Thread Design with HP Multi Jet Fusion
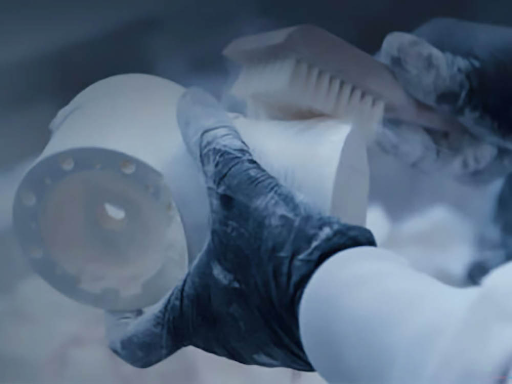
Designing for HP Jet Fusion
HP Multi Jet Fusion (MJF) has redefined what’s possible in 3D printing, allowing for the creation of highly accurate, durable, and production-ready components. While the technology offers speed and efficiency, designing for MJF comes with its own set of challenges—particularly when it comes to achieving the right fit and threading.
Unlike traditional machining, where tolerances are controlled with extreme precision, additive manufacturing introduces factors like material shrinkage, powder spreading, and thermal expansion, which can affect how components assemble and interact. Engineers working with MJF must carefully design for these variables to ensure functional, high-performance parts.
Understanding Fit in HP MJF Printing
Dimensional accuracy in MJF is crucial for parts that need to fit together seamlessly. Traditional machining allows for ultra-tight tolerances, but MJF typically operates within an IT10–IT12 range, which is suitable for engineering-grade fits but may require post-processing for higher precision applications.
Achieving the right fit means considering how parts will interact. A clearance fit allows for easy movement, making it ideal for components like bearings or sliding assemblies. An interference fit creates a secure hold, commonly used for press-fit applications where parts need to remain fixed under stress. A transition fit falls between the two, offering a balance of easy assembly with some degree of friction or force holding components together.
One of the key considerations in MJF design is compensating for shrinkage and cooling effects. Parts often contract slightly as they cool after printing, meaning designers must scale up dimensions slightly—typically by one to two percent—to achieve the correct final size. In some cases, pilot holes are pre-designed smaller so they can be drilled or bored to final specifications in post-processing, ensuring higher precision and smooth assembly.
Challenges of 3D-Printed Threads
Threads are an essential feature in many 3D-printed parts, allowing for repeated assembly and disassembly without compromising structural integrity. However, MJF-printed threads present unique challenges compared to their machined counterparts. Fine details, especially in threads smaller than six millimeters, may not resolve properly due to the layer-based printing process.
Thread strength is another key concern. Printed plastic threads may not be durable enough to withstand repeated use or heavy loads. Powder residues from the printing process can also affect thread engagement, requiring additional cleaning or finishing. Engineers must carefully select the right threading method to ensure long-term performance.
Choosing the Right Threading Method for MJF Parts
Designing threads for MJF involves multiple approaches, each with its own advantages. Directly printing threads is a cost-effective option, but it works best with coarse thread profiles and larger diameters. To improve engagement, a small clearance gap is necessary to prevent binding. While this approach eliminates post-processing, it is best suited for low-stress applications.
For more precise, durable threads, machining them after printing is a preferred method. Internal threads can be tapped, while external threads can be cut using a die. This approach ensures high accuracy and smooth operation, making it ideal for smaller threads or high-performance applications.
Another option is to use self-tapping screws, which can be installed directly into pilot holes printed in the part. While this method provides a strong hold, it is best for applications where threads do not need to be repeatedly engaged and disengaged.
For high-load applications, threaded inserts are the best solution. These inserts are placed into the printed part using heat, ultrasonic vibration, or a press-fit method. They provide a reusable, high-strength thread, making them the ideal choice for frequent assembly and disassembly.
Post-Processing for Superior Fit and Thread Performance
To enhance the performance of threads and ensure proper fit, post-processing is often necessary. Powder residue left behind from the MJF process can interfere with engagement, requiring cleaning techniques like sandblasting, compressed air, or ultrasonic cleaning to remove excess material.
For parts that will undergo repeated use, coatings such as lubricants or dry films can be applied to improve wear resistance and smooth operation. Coloring is another consideration—dyeing is generally preferred over painting since paint buildup can interfere with thread engagement.
Designing for Strength, Functionality, and Precision
Getting the best results from HP Multi Jet Fusion requires an in-depth understanding of material behavior, printing tolerances, and post-processing techniques. Whether designing for clearance fits, interference fits, or highly durable threaded connections, engineers must account for shrinkage, surface finish, and reinforcement strategies to ensure functional, long-lasting parts.
For businesses looking to optimize their MJF designs, working with experts in additive manufacturing and material science is essential. At RapidMade, we specialize in high-performance 3D printing solutions that ensure precision, strength, and efficiency.
For expert advice on designing for fit, tolerances, and threads in HP Multi Jet Fusion, trust the 3D printing service at rapidmade.com to see how we can help bring your designs to life!